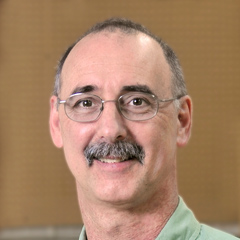
DIY Countertops
George VondriskaHere’s a great DIY upgrade you can do for your camper, or your house. Make your own countertops. We’re installing sinks from Lippert in the galley and bathroom, and a very nice Lippert faucet in the galley. Follow along the step-by-step process of making your own countertops.
Sometime ago, as part of this project, the countertops came out of here and the bathroom, and in addition to the countertops coming out, there are new sinks going in. So we are going to fabricate new countertops. This is something you can easily DIY do. The stuff we're gonna use for this is home center available. Here at the camper, measure what you got going here so that we can anticipate the size of the new countertop.
We want that countertop to overhang front and the end. In this case, it's blind on that end, it goes up against the stove, but it will overhang on this end. So later, I'll talk about the core of the countertop, and then that's gonna get an edge on it. We want the core to overhang our cabinets by a 1/4-inch off this end and a 1/4-inch off the front. That's the core.
And next, we can look at just what it's gonna take to fabricate this and get it installed. Here in shop. Let's build a couple of countertops. The core of the countertop, for that material, particle board is a time-tested countertop core. I'm using 1/2-inch material for the camper.
If I were doing this for a typical kitchen, bathroom vanity in a house, I would be using 3/4-inch material, but as a weight consideration for the camper, I went with 1/2-inch. You can get 1/2-inch particle board at home centers very, very easily. It's an inexpensive product, and it also lays really, really flat. That's one of the big benefits for p-lam for the plastic laminate work. So I've got my dimensions, and remember, we want our core to be 1/4-inch deeper and 1/4-inch longer than the cabinet it's going on to.
Table saw's easiest way to make that part happen. Now in addition to the countertop component itself, We end up putting a little rails, kinda cleats, under the countertop, just right around the edges. There's just kind of a band that surrounds the edges. Commonly, those are two or three inches wide. So from the off cuts I have, now I'm gonna rip some of those rails some of those cleats.
While you're here, at the table saw. The way this is all gonna come together is we're gonna have our particle board core, plastic laminate over the top. More on the plastic laminate in just a second. And solid wood banding on the front and the edge. So while we're at the table saw, to match the other stuff, I've got to go in the camper, I'm gonna use pine for my solid wood banding.
So I'm gonna rip that while I'm here, I make this banding a quarter inch wider than the net thickness of the countertop. So my core is gonna be one inch thick when I'm done, 'cause I got a top layer and then those rails. And so I'm gonna make this one and a quarter. And now while we're at the table saw, we can also take advantage of this in order to cut the laminate to size. I just gotta go get it.
First off, let's talk about plastic laminate. A lot of people just call it p-lam, plastic laminate. You can get into stuff at home centers. And if you go in and have a look, generally they have some stuff on hand. If they don't have what you like on hand, they can generally order it.
So it is just what it sounds like it's plastic and it's about a 16th of an inch thick. Be careful as you're handling it, 'cause the edges can be really, really sharp. And it is easy to accidentally cut your hand with it. We can cut the stuff on the table saw, but the problem is with most table saw fences, there's just a little bit of a gap there. And if like the particle board I just come to the fence and do this, it's gonna wanna slide under there.
So it's a simple solution. Grab one of those other pieces that you've cut, put that up against the fence. And now when we approach this with the laminate, it's gonna ride on top of that. So once we're set up to do that, We can make our cuts. You want your laminate to end up being an inch bigger in both directions than the finished core.
So make sure that you're accommodating the edge banding when you cut these pieces to size. Otherwise they're gonna end up too small. Thing you may have noticed is that I'm being a little bit careful handling this, one, sharp edges, like I mentioned, but two, if you bend it too much, there's a point where it's gonna snap and it's easier with a big piece like that. If you just kind of let that cantilever out from your hand, there's a good chance it's gonna break and you don't wanna do that. So I'm pretty careful keeping that plastic laminate supported as I move it around to make sure that I don't get a crack in it.
This countertop core is already done. It looks the same from this perspective. But when we do this, it's more than just a sheet of particle board. Now it's a countertop core 'cause I've got those rails fastened to the bottom that we talked about a little bit. So it's a very simple step.
All we're gonna do is glue and staple those in place. As you put this stuff together, these rails are cut so that they match the length of this piece. We want these ends to be flush. As I put the rails on, I'm making sure that they're flush across the edges, 'cause the next thing that's gonna happen, like literally the next thing, is that edge banding is gonna get applied here. So you wanna make sure that the surfaces are even so we can fasten that pine, in this case, that edge banding onto there.
That takes care of this part of the core. And like I said, now we're ready to band these edges. The banding is ready to go onto these cores. And what I'm doing on mine, is I've got this corner mitered. Don't sweat this step at this point.
We're gonna talk about that in a second. If you don't want to, or you're not able to miter yours, another way to do this is to just let the banding pieces bypass each other. So if it were me, I would have the short side even with the front and then have the longer front piece. Come past it like this, and that's not a bad look, either. And it's a whole lot easier to do, but if you can pause and pass the miter saw, then you can get that miter on there.
Now what's gonna happen with these is, this is sitting here, right side up. We know that the banding was made to be the wider than the core is thick. But look at how this one is set up. This one is already glued. So it's sitting here upside down and there's a method to the madness there.
Gluing it upside down, makes this a whole lot easier to do. So I'm gonna get this guy pushed out of the way, and then we're gonna do that same press to this one. Now, one of the things you have to pay attention to is you probably have a right and a left. So in my galley, I need my finished, banded end to the left. In my bathroom, I need my banded, my finished end to the right.
This is the bathroom one. So when I'm done, this would be correct. So I'm gonna do this and I'm gonna do this. And that's gonna give me the look I want. Bunch of clamps laying here.
And one of the benefits of doing it like this, it makes it easier to get the banding on. And then two, it makes it easier to get clamps on. And if you've got clamps and can do it this way, then you don't have nail holes in this banding that you have to fill later. You can get a clamp ready but I'm not gonna put it on, 'cause one of the things I'm gonna look at is I'm gonna bring this piece in. It doesn't have glue on it yet, but I'm just using it to show me where this piece has to go in order to make the miter work.
So this piece is simply locating the front one, the one that's on my side. Right there in the miter looks cool. Then I can span that, double check. Now as I close the clamp. The reason that we're upside down is I'm pushing on the core and pushing on the banding, everything that is referencing off my bench stop.
So I have to hold them flush or close to flush. And then from there we can use clamps. On this band, I'm gonna add clamp pads because the clamps going this way, do you have pads on them already. But bar clamps, the plate clamps going this way do not. And I don't want to mar my band.
Close the miter. Push down. That's it. We're gotta let that dry before we're ready for the next step. Once the glue is dry on edge banding, we have a few more things we need to do before we can do the p-lam on top of it.
One of the things you might have noticed, is that I let my banding just run wild. I let it just stick past the edge of the core. And I find it's often easier instead of trying to cut that to exact length, especially with a miter on this end, to just cut it after the fact. Very simple to do that with a handsaw. And what I'll do here is push the saw against the core like that, and then cut.
And 'cause my fingers are holding the saw there, this is a pull saw, I'm basically tracing that edge for the cut. Boom. Nice. The other thing we have to pay attention to is the fact that it's possible that when you put your edge banding on it didn't end up perfectly flush with the top. And any whoop-de-doos that you have in the surface of the core or the banding are gonna telegraph through the laminate and it won't be flat.
Little countertop like this, it's probably not too big a deal. But if you ever get to where you're doing a big countertop, the more ups and downs you have, the more obvious it's gonna be. It's already been taken care of on this one. This has been sanded. You need to do the same thing to this one.
One of the things we want to stay away from is any opportunity to dish this thing out. We wanna sand it uniformly. So easy way to track that is to take a pencil and do this. And then I'm gonna use a random orbit sander. It's a six inch sander and I'm gonna run it over the top of this.
One of the things that you wanna make sure of is, you know, it's easy, especially when you get to where you're kind of in a hurry. You wanna lean on it in one spot. You wanna tip it and try to like encourage it to sand a little bit more there, not a good idea. We wanna keep this flat. So keep the sander nice and flat.
The idea with the pencil marks is I'm gonna move uniformly, taking those pencil marks off. And if they're all gone and I have more sanding to do, I'll just take the pencil, hit it again and sand again. Our end goal is to get that banding perfectly flush all the way around and any glue beads that squeezed out, came out, we wanna get rid of those too. Once the lines are gone, a little finger test. They gotta be flush.
These surfaces gotta be flush. In this case, they're done. I have flush-icity right there. This is nearly ready for plastic laminate. One more little step.
This was the one more thing we had to do before we were ready for glue and plastic laminate. You've gotta make sure that these surfaces are dust-free. We just got done sanding them. And you can't have that find saw dust on the core or on the plastic laminate itself. The other thing I've done to get ready here is I put rosin paper down on my bench.
So if/when I spill a little bit of glue, it's not gonna end up on the bench. The glue for this is a whole different kettle of fish than wood glue. We're using contact adhesive and contact adhesive is interesting stuff. Normally we put glue on a surface. We put the two items together while the glue is wet, they cure over time and then they're stuck together.
With contact adhesive what we're gonna do is we're gonna roll it out onto the core and onto the p-lam, let it dry, then stick them together. This particular product is a solvent base contact adhesive, if you're using solvent base, you gotta make sure you've got really, really good ventilation going, because it is highly flammable. So there's an exhaust fan running in here right now. Getting out the gross air bringing in fresh air. There is water-based contact adhesive available.
So if your environment is not at all conducive to all the parameters that are set up, read the directions on the can, then you can use the water-based stuff instead of the solvent based stuff. At this stage of the game, roll it out on the core, roll it out on the p-lam and then we'll be ready for the next step. Now look at our two cores and you can see that there are some pretty obvious dry spots there. All of this area here is quite dry. So if that happens to you and it's likely it will 'cause particleboard soaks up a lot of glue, then you need to hit the cores again.
I don't anticipate having to do the p-lam again, 'cause it's not as absorbent as particleboard. Now we watch glue dry. Contact adhesive, read the instructions, it's funky stuff. We want this to be to a point where if you touch it, it's just a little bit tacky. Then we're ready to put these two surfaces together.
Right now, they're way too wet. Once the glue is dry. So it's got just that tiny bit of tack to it, we're ready to put these together. Here's the really, really, really important thing about this. Once that touches that it's a one-shot deal.
They're gonna be stuck. So you wanna be really careful about getting this flipped over and on this surface, if this was a bigger countertop, I'd have somebody here helping me so that we could make sure everything was in the right spot. Even with a bigger countertop and another pair of hands, I would be doing this. These dowels are gonna prevent these surfaces from touching, until I'm ready for them to touch. So again, even if I had somebody helping me, I'd still be putting the dowels on here like this.
Then we'll take this, flip it, get it on the dowels. So they're currently not in contact. Now, if this had like a wood grain to it, it'd be really important that right now we could manipulate this and make sure that the wood grain or whatever pattern you've got is parallel to the edge of your work. I wanna make sure I have a hangover, overhang on every side. Then take out one dowel, make contact, work your way down.
One of the things that's really important is your environment too. So if anything falls out of the air, like a little chunk of dust or something and gets in the middle here. When you do this, you're gonna feel a little bump. So you really wanna keep your working environment clean. And that's already pretty well stuck, but we're gonna go one step further.
This thing is called a J-Roller. And the way it works is that it's gonna roll the surface out. And as I lean on this, it puts all this pressure concentrated into one little spot. So this is a great way and a must have in order to get these two surfaces pressed together and make sure you have complete contact. And I really concentrate on these edges To make sure that those have come together.
This whole thing gets rolled. I'm gonna get those two together. That's the bathroom countertop. I'm gonna get that assembled. Finished, rolling this.
Roll that and then this aspect is done, but we now have to cut the laminate to match the core. The easiest, and honestly, the best way to get the laminate perfectly flush with the core, is to use a flush trim router bit. This bit has one portion that's gonna ride on the core and then a cutter that's gonna cut away anything that sticks past. It's a really good idea to put masking tape on the base of your router. If anything is sticking up, that could easily scratch the laminate.
So it could be just a little high spot in the base. It could be a screw head in the base. Don't take the chance. 'Cause if you get a scratch in this laminate, you're gonna be starting all over again. Now the beauty of this and the way this works is that all we have to do is get that non cutting portion of the bit up against the core and come all the way around.
It's gonna end up perfectly flush. Now same thing to that one. And then we have one more decorative detail to do to these. One more step here to wrap up and dress up our countertops. This is a really, really nice detail.
Here in the router, I now have a chamfer bit. Router's unplugged. Masking tape stays on. That chamfer bit is at a 45 degree angle. And so when we run that around the edge of the countertop, that's gonna cut partially into the laminate, partially into the pine.
And I really like the look that that gives, the transition it creates between the top of the countertop and the vertical, the banding that we've put on. Only do this on the sides you have banded. Don't do this on edges where it's only particle board. Isn't that great. Look at that edge.
I love that look. Gotta do the same thing for this one. Now from here, a little bit of sanding on the banding and then get a coat of finish on there. The Aquathane that we put on the wainscoting would be a great choice for this, that same product. Get that sealed up.
And then we go look at what it's gonna actually take to get these into the camper. We're getting down to the final stages here on these countertops. What you need to do is figure out where you're gonna locate your sink on the countertop. And once you've got that figured out, the best thing to do is put masking tape on there and then trace onto the masking tape. Masking tape is gonna do a couple things.
In this case where that laminate is so dark, it's much easier to see the line on masking tape than it would be on the laminate. And then we're gonna get to a point where we're cutting this with the jigsaw and that laminate around the masking tape is gonna help prevent chipping that we might get from the saw. Now here's the thing, I've located the sink. This is the galley countertop and the galley sink. And when I trace that, the line that we have is the outside of the sink.
Don't cut there. The whole premise with this is that this is gonna suspend. It's gonna sit on this lip and hang into the countertop. So what we need to do is move that line in. And this is a really great trick for tracing stuff or scribing stuff.
The trick is I'm gonna take a piece of scrap and put it on the sink line. And then I'm gonna put a washer up against that. And with my felt tip inside the washer, I'm just gonna ride that along. Now, when I get to the curve here at the end, I need to stop. And we'll just deal with that in a second.
But what's neat about this is that washer automatically gives me a setback from the edge and it's gonna give me my actual cut-line on the inside. And then on these rounded corners, what I'm gonna do is just this. I've got a starting and a stopping point coming off of the lines that I created with the washer. So coming off of those, I can just spitball that curve. Like that.
One of the things that's worth pointing out is I've got a pad sitting on the countertop, 'cause I've got tools sitting here and I want to make sure that the tools are on that pad. Not on just the countertop. I don't wanna take any chance at this stage of the game, that I'm gonna scratch that plastic laminate. All right. I think we're set.
Gonna punch a hole so that my jigsaw has a place to start. The other benefit of my masking tape. Remember that we put masking tape on the base of the router. So now here with the sole of the jigsaw on the p-lam, I'm protecting the laminate from any scratch potential from that jigsaw base. Choose the right line here, the correct line, not the right line.
Tip here, when I've got to a point here where I'm gonna stop and I'm gonna come back and cut this way. When you turn that jigsaw off, don't turn it off while it's still coasting down, take it out of here. 'Cause I've had it happen so many times where I've done that. And if the bottom of that blade hits the surface while it's coming out, or if you don't turn it off, and you try to just lift that out of there with it running. If it has the opportunity to bounce around on that surface, it's really, really bad.
So let it come to a stop down in the cut, then take it out. I had about a million things going at the end there. I wanted to support this so that when it gets to the end of the cut, it cuts through and doesn't just fall and crack the laminate. And then just from the way my countertop was sitting on the saw horses, remember, we've got those rails underneath there. And it slid off of the rail, gave me a little startle, reflex action there.
Now what's going on here is these bolts are fastened to the bottom of this thing. So let's check and see, did I clear the bolts? Yup and this is cool. This is what we want. I want to have a little bit of wiggle room there so that you can get that exactly where you want it and then fix it in place.
Fix it in place is gonna be... there's hardware here and that hardware is gonna go onto those studs. The rubber ends come off and then once that's on here, that's basically flanges that are gonna fasten up from the bottom to hold that in place. So the tape comes off. We've got to put caulk on here and caulk that in place.
Then the other thing I'll do is now that I've got this cut in, my faucet gets located back here. So I'm gonna correctly locate that faucet. That "X" is just a spitball. And once I know where it goes, this just gets a hole drilled for this base. It's a very easy install.
Drill a hole, put that through the hole. Part of where I'm going with this, is that, anything that we can do, while this sink and the other sink are here. It's way easier. You saw me take the old sink and the old countertop out and crawling underneath there and doing connections and all that stuff is a pain. So don't set your countertop, then cut the hole, then put the sink in.
Do all of this stuff in this kind of an environment. And then it's gonna be a whole lot easier. At the end of the day, all I'm gonna have to do is pick this whole thing up, set it over the base cabinet, make the final connections, everything, but the drain, 'cause that's rigid, but I'll be able to do the water supply-line connections before the countertop is fastened in place. Then fasten the countertop, hook up the drain, it's gonna be done. So just remember anything that you can do outside of the cabinet environment, do outside of the cabinet environment.
I am going to get this faucet in, then I'm gonna do the vanity countertop for the bathroom. And then you got to think a second. I think we'll be ready to head back to the camper, at that point. You know, there are a lot of upgrades to this camper that I really, really like, but this is one of my favorites. Great faucet, great sink from Lippert, same in the bathroom.
And with this new countertop in here, the additional real estate that we've got here, what a wonderful change to this camper. Now, the way this has been put together, the laminate on top, the pine on the edge. One thing I like about that is from here. I can see the wainscoting that was put on those walls earlier. I love how the pine matches the wainscoting over there.
It ties everything together. With this particular faucet. I like that now, we've got the space over here and I can take advantage of this to fill stuff like my coffee maker, that might be over here on the countertop. Lot of good stuff going on. It's such a wonderful, better look from what we had here.
And couldn't be happier with the way all this shook out.
Outstanding instructor, great how he took his time with each step in the process and gave tips to help prevent us from making mistakes. GARY
Good job --- looks great!